Reação Álcali-Agregado (RAA): ela pode afetar o pavimento ou piso de concreto?
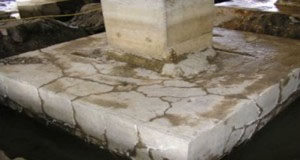
Quando ouvi falar a primeira vez da reação álcali-agregado, era o tipo de preocupação que ocorria – ou pensava-se que ocorria – principalmente em obras com de concreto massa, com grandes volumes de concretagem como, por exemplo, em barragens ou grandes blocos de fundação. As condições necessárias para a ocorrência delas estava ligado à presença de agregados reativos, cimentos com alto teor de álcalis e temperatura elevada, como as que ocorrem em barragens devido ao calor de hidratação do cimento e que perduram por muito tempo.
Não se pensava que uma fundação convencional, um pilar de concreto ou mesmo um piso de concreto pudesse estar sujeito a esse tipo de problema. Porém, hoje sabemos que ela não é tão limitada e sua ocorrência tem sido mais comum do que imaginávamos. Há ocorrência recentes desse tipo de reação em obras do nordeste (Pecchio ET AL, 2008), nas quais não há ligação direta com grandes volumes de concreto (a figura 1 apresenta bloco de fundação atacado pela RAA) e no último ano, foi detectado problemas no Ginásio Aecim Tocantins, obra recente, de 2007, com arquitetura moderna e estrutura arrojada, cujos pilares principais de concreto apresentaram essa patologia (Valin Jr et al, 2014).
Mas, o que é a RAA? Em poucas palavras, é a reação química que ocorre entre alguns tipos de agregados e espécies (compostos químicos) alcalinas existentes no cimento ou que são introduzidas no concreto por fontes externas. A sua ocorrência está condicionada a: existência de álcalis (sódio e potássio), agregado reativo e umidade.
Os agregados do concreto eram, no passado, considerados inertes, isto é, a presença deles não afetava as reações de hidratação do cimento Portland, nem havia reação química entre os produtos de hidratação ou espécies (compostos químicos) do cimento e os agregados, que eram até denominados por “inertes”. Por volta de 1920 a 1930, foi pela primeira vez observado na Califórnia (EUA) esse tipo de reação química, tendo sido comprovado a ocorrência de reação entre os álcalis do cimento e a sílica – agora denominada “ativa” – dos agregados. No Brasil, os primeiros estudos sobre o assunto realizados por ocasião da usina hidroelétrica de Jupiá, ainda na fase de projeto, tendo sido tomadas medidas preventivas para o seu controle.
Hoje sabemos que há três tipos de reação álcali-agregados: álcali-sílica, álcali-silicato e álcali-carbonato; ambas produzem o mesmo efeito ou dano no concreto. O interessante de cada uma é o tipo de agregado em que aparecem: a álcali-sílica (RAS) em agregados que contenham opala, cristobalita, vidro vulcânico, etc; álcali-silicato ocorrem em rochas que foram submetidas a processos tectônicos (metamórficos), ou seja, sofreram ao longo do tempo processos de dobramento ou outros que geraram quartzo tensionado, como o gnaisse (comum na região da serra do mar), ardósias, filitos, quartzitos, etc; finalmente, a reação álcali-carbonato (RAC), que ocorrem com calcários dolomíticos (que apresentam óxido de magnésio com espécie importante).
Para nós, o objetivo deste texto não é adentrar profundamente nas reações mencionadas, mas apenas dar conhecimento da existência delas e o que podemos fazer para evitá-las ou promover a sua mitigação, ou seja, sua possibilidade de ocorrência. Não temos conhecimento da RAA em pavimentos no Brasil, mas no exterior, já há relatos de pavimentos deteriorados após 5 anos de execução (Hong et AL, 2007) e portanto, devemos atentar para a possibilidade de ocorrência, principalmente em pavimentos externos, onde as condições da reação – temperatura e umidade – estão presentes.
O maior problema para o construtor é saber se a rocha que vai ser usada como agregado é reativa ou não; uma primeira estimativa pode ser feita a partir do histórico de sua utilização. Por exemplo, determinada pedreira produz agregados para concreto há mais de 20 anos e nunca ouve problemas, pode ser uma alternativa para tomada de decisão, dependendo do nível de risco e consequências da expansão. Esse procedimento, do histórico do desempenho, nem sempre é possível, ou comprovável, pela falta de registros precisos. Daí, a saída é buscar procedimentos mais científicos, como a análise petrográfica e os ensaios de expansão para determinação do potencial reativo do agregado, sempre com o auxílio de um profissional experiente, ou já buscar soluções preventivas para inibir a reação, mesmo com agregados reativos.
Pela natureza da reação, que é pozolânica, o controle da reação álcali-sílica é feito com a adição de materiais pozolânicos ao concreto, como a cinza volante, pozolanas naturais, microssílica, metacaulim ou mesmo escória de alto forno, que em função da finura e reatividade combinam rapidamente com os álcalis formando espécies não expansivas.
A NBR 15577-1 apresenta modelo de análise de risco de ocorrência da RAA, levando em consideração as condições de exposição, dimensões do elemento de concreto e responsabilidade estrutural, e a partir daí, classifica as ações preventivas em: desnecessária, mínima, moderada e forte; no primeiro caso, o agregado pode ser aceito sem verificação do seu potencial reativo, enquanto que nos demais casos este deve ser avaliado. Nos diversos exemplos de estrutura considerados na norma brasileira, não há menção aos pavimentos.
Similar a ela, temos a norma americana ASTM C 1778, que já classifica os pavimentos como SC3, que enquadra os elementos estruturais nos quais há problemas significativos de segurança, além dos ambientais e econômicos; imaginamos que esse tipo de estrutura (não maciça e em contato com água) se enquadraria no nível moderado quanto à ação preventiva descrita na norma NBR 15577-1.
As medidas de ação preventiva moderada são: utilizar concreto com teor de álcalis inferior a 2,4 kg/m³ ou utilizar cimento CP III (mínimo de 60 % de escória) ou CP IV (mínimo de 40 % de pozolana) ou empregar os materiais cimentícios citados anteriormente. Para os pisos industriais, mantidos em ambientes secos, pode-se adotar as medidas de ação preventiva mínima, que abrangem: teor de álcalis do concreto menor que 3,0 kg/m³ ou empregar cimento CP II – E ou CP II – Z ou uma das medidas da ação moderada, mas devemos lembrar que essas medidas só são necessárias quando os agregados são potencialmente reativos.